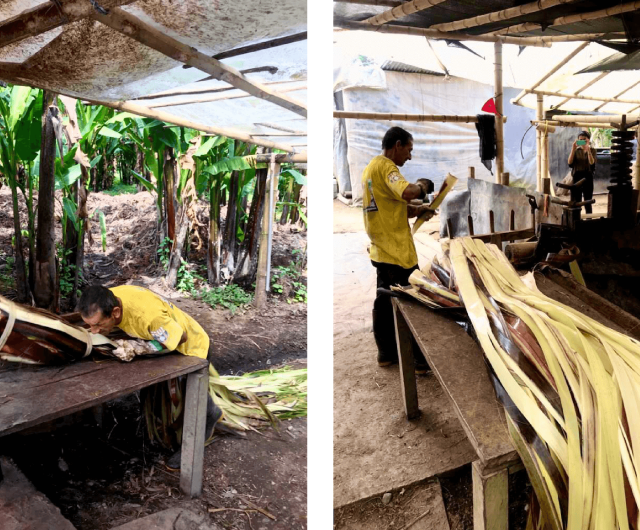
Abaca filters win Made by Project first prize
MADE BY PROJECT is an international competition designed to seek out the innovations of tomorrow, and to support and promote socially responsible inventions in the coffee industry. Discussion published in Standart Magazine, issue 24, with Laure Jubert.
The 2021 edition attracted an impressive field of 30 high-profile entrants. Can you tell us about a few stand-outs?
The submissions covered a range of areas, including phone apps and other technologies that can revolutionize the way our industry works. We also learned about the future of coffee consumption, given that many projects addressed the issue of how to reduce single-use products and up-cycle the waste produced from brewing and roasting. Overall, we loved all finalists’ projects, and plan to follow them closely (even though for now, we have to keep them secret!).
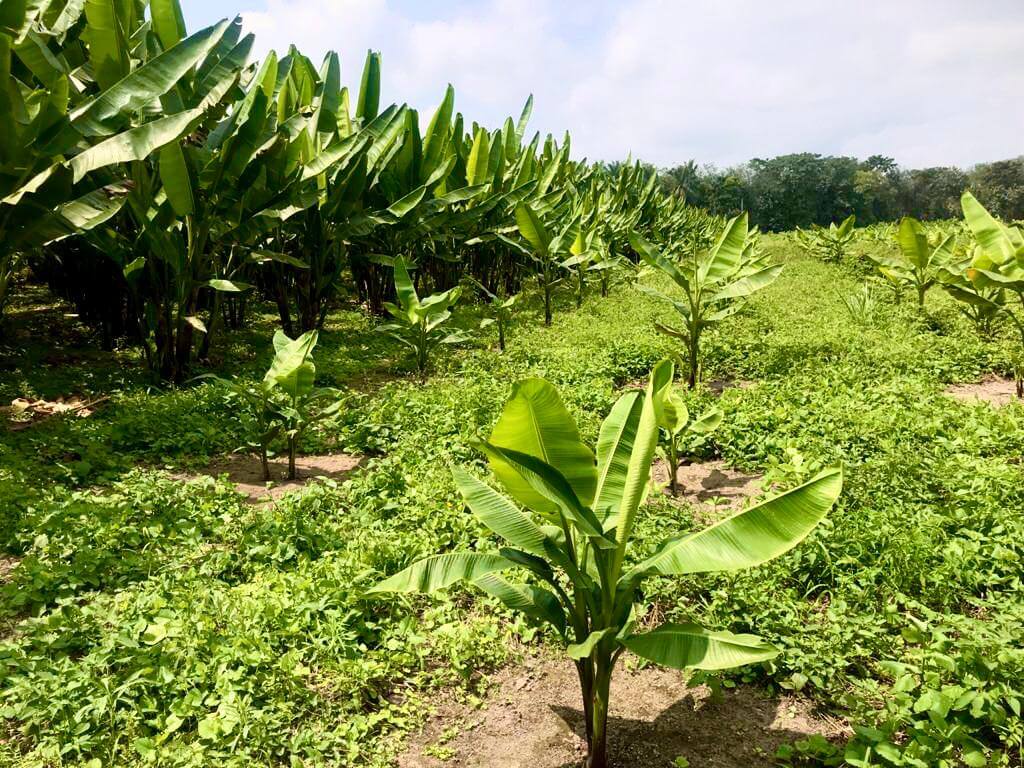
The 2021 winner was Arnaud Causse, who is working to produce filters made from abaca fibre in collaboration with a farmer in Ecuador. Could you tell us a bit more about this project?
First, it is important to state that this innovation would raise value and sustainability throughout the entire production chain. When you really dig into the world of coffee filters, you realize that it’s very hard to get hold of transparent information, especially concerning who produces them and how!
What impressed us most about Arnaud’s project was his idea of extending to abaca producers what is already the case for speciality coffee: fair prices, and sustainable and fair working conditions. It is also the first time that a product featured in our Equipment catalogue will be harvested and processed on-site in a coffee-producing country, and above all, it would allow our partners in Latin America to order filters and purchase equipment more easily. Everyone has a right to utilize the latest innovations, not just the countries of the Global North.
'Abaca is produced on soil that is not suitable for other types of agriculture, and therefore does not compete with or encroach on food-growing areas.'
Arnaud has been involved with abaca since his first trip to Ecuador in 1989. He observed large plantations of banana trees that did not grow any bananas because they were being used to make fibre, but even so, it had not become popular internationally for reasons that are difficult to understand, given that the abaca fibre possesses extraordinary properties. It is very long, unlike cotton, and is very resistant, especially to seawater, so has traditionally been used for ropes in boats.
Today, abaca plantations are mostly to be found in the Philippines, Ecuador, and Costa Rica, but more than 90% of the global market is captured by just two companies, and unlike the textile industry, which has generated a lot of attention about workers’ conditions, this monopoly means that the majority of abaca producers work completely outside the public eye in extremely precarious conditions, including slavery.
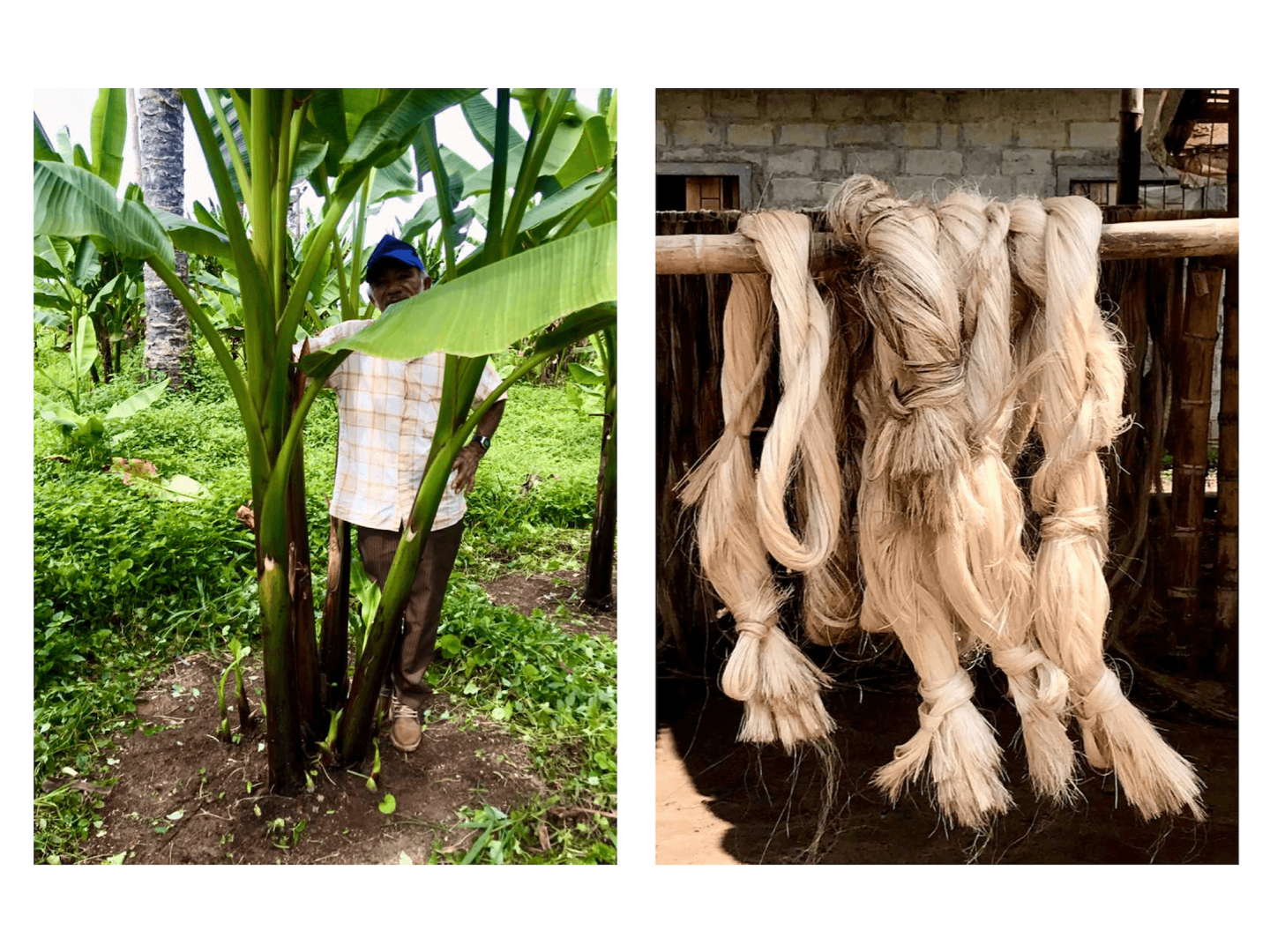
Why is abaca better than paper for filters?
Abaca creates high-quality cellulose that does not need to be bleached with chlorine, which leads to an almost-white filter that does not have to be put through a chlorine bath. The idea for the project first emerged among baristas, who are familiar with the subject of filters and tend to prefer abaca to paper, which always has a taste, especially after chlorine bleaching. Abaca, however, is completely neutral, and will not add any unwanted taste to your extraction.
It is also much more environmentally responsible to produce abaca than paper. Abaca is produced on soil that is not suitable for other types of agriculture, and therefore does not compete with or encroach on food-growing areas. The abaca plant is more sustainable than paper because it can be harvested more often, and when you cut off a bud to make fibre, two others will grow in its place. The trees used for paper filters grow much more slowly.
Causse’s idea is to partner with a producer who farms about 20 hectares. This plantation is located at the foot of the Andes, at an altitude of 500 m in the coastal zone of Ecuador, where clouds from the Pacific accumulate. It is roughly 50 km from Causse’s own Las Tolas plantation, which is on the same side of the Andes but at a much higher altitude of 1800 m. All of Causse’s employees are fully insured and receive a salary that corresponds to international best practice. He also ensures maximum traceability so that coffee lovers can trace the supply chain that has brought abaca filters to their shelves, and can verify that no exploitation has taken place.
Several examples of Causse’s commercially available filters have been sent to a university in Ecuador to improve their design, and the prize money awarded in the contest (€5,000) has been entirely donated to this university to enable the students, engineers, and researchers to work on them. The analysis of the samples is already under way, and it turns out that even the filter sold as ‘100% abaca’ contains about 4% ‘soft’ pine cellulose fibre. The project will now study how the filters have come to include non-abaca fibre (it was certainly not to reduce manufacturing costs).
We’re going to make a filter for Chemex because their filters are simply a disc that doesn’t require a weld, unlike the V60 filter. (A weld doesn’t require advanced technology, but you do need the machine!) We will start with five or six prototypes to perform a series of tests with baristas, and thereby select the filter that yields the best extraction. It’s possible that several filters will result, based on the type of extraction, the coffee involved, and the method of preparation employed.
Did you like this article? Share it with your community: